Screw compressor
Zhejiang AGKNX Compression Equipment Co., Ltd. introduced the French AGKNX high-end screw compressor manufacturing technology to digest and absorb in China. It is the first domestic high-end screw compressor manufacturer that uses water for cooling and lubrication inside the compressor. It is the first to launch the two-stage compression high-pressure micro-oil screw compressor within the scope, and the pressure reaches 4.0Mpa; then the world’s first 4.0Mpa pressure oil-free screw compressor and the world’s first 1.25Mpa pressure oil-free scroll compressor are developed. AGKNX’s R&D team constantly challenges and breaks through the highest technology of air compressors, and constantly creates the most advanced compressor products in the world. Based on this advanced technology and precision manufacturing, the oil-injected screw air compressor produced by our company has a high volumetric efficiency ratio, high temperature resistance, durability, and energy-saving effects.
COMPANY INTRODUCTION & EVER-POWER
The company has strong technical force, advanced production and testing equipment, and strict implementation of the ISO9001 quality management system. The products have obtained the EU CE certification, and the oil-free machine series have passed the German authority TUV Class 0 testing. The existing professional R&D team is continuously conducting the development and research of compressor energy-saving technology, and has obtained a number of international and domestic inventions and utility model patents. The company adheres to the enterprise spirit of “strict management, enterprising, good innovation, trustworthiness, and service”, adheres to the development path of high, new, and professional, adheres to the people-oriented thinking, and implements “there is no best, only better” R&D and manufacturing Philosophy, pursuing the realm of “zero defects in products and zero distance in service”, through scientific management, technological innovation and brand services, we will continuously improve the company’s comprehensive operational capabilities and market competitiveness, and strive to build a strong brand of “AGKNX”, dedicated to the Chinese compressor industry Contribute to the revitalization and development of China.
A Rotary Screw Air Compressor is a compressor that uses a rotary-type positive displacement mechanism, called a rotary screw, air-end. Rotary Screw Compressors are commonly used to replace piston compressors, in commercial and industrial applications, where large volumes of high pressure air are needed. Another name used (though not frequently) is “twin screw compressor”.
The compression process of a Rotary Screw is a quite different than that of a reciprocating piston compressor, as the Rotary Screw air-end generates compression in a continuous sweeping motion. There is very little pulsation or surging of flow, which occurs with piston compressors. Rotary Screw Compressors also use two inter-twined helical shaped screws, known as rotors, to compress the air. These rotors are precision machined to extremely tight tolerances, whereby the vanes on the rotors are almost touching, and typically just a few thousandths of an inch apart.
In an oil-flooded Rotary Screw Compressor, lubricating oil bridges the space between the rotor vanes, both providing a hydraulic seal and transferring mechanical energy between the driving and driven rotor. Air enters the system at the “suction side” of the air-end and moves through the rotor vanes as the screw rotors rotate. The inter-twined rotors force the air and oil through the air-end, which eventually exits at the end of the screws. The air and oil then go through a separation process. The air is cooled and routed to air lines and a receiver. The oil is also cooled, filtered and re-routed back into the air-end in a closed loop system.

We carry a wide selection of Rotary Screw Air Compressors to meet the needs of every application Buy online or call our knowledgeable staff to help you find a compressor to suit your needs.
When it comes to the screw type air compressor, generally, there are two kinds, single-screw type and twin-screw(or double-screw) type. We will make a comparison between these two kinds of air compressors.
Differences | Single-screw air compressor | Twin-screw air compressor |
---|---|---|
Structure |
A screw rotor and two symmetrically starwheels.
The screw groove and the inner wall of the casing constitute a closed elementary volume. So that the gas can reach the required pressure.
It has the characteristics of simple structure, small volume, and so on.
|
The twin-screw compressor is a double-shaft positive displacement compressor.
The main (male) pair (female) two rotors cooperate to form a meshing pair.
The tooth profile of the main and auxiliary rotors forms a closed elementary volume with the inner wall of the casing.
|
Working principle |
The motor transmits power to the screw shaft through coupling or a belt. The screw drives the star wheel to rotate.
The gas enters the screw groove from the suction chamber. The exhaust port and the exhaust chamber compress the gas, and it is discharged.
The role of the star wheel is equivalent to the piston of a reciprocating piston compressor. When it moves relative to each other, the enclosed volume is gradually reduced. Then the gas is compressed.
|
The motor drives the main rotor through a coupling, speed-increasing gear, or belt. The main rotor directly drives the auxiliary rotor to rotate together.
Under the action of relative negative pressure, the air is sucked in. The gas is transported and compressed under the anastomosis of the tooth crest and tooth groove.
When the rotor meshing surface turns to communicate with the exhaust port of the casing, the compressed gas begins to be discharged.
|
Technical history |
The invention of the single screw type is more than ten years later than the twin-screw type. | The invention of the twin-screw compressor was earlier. |
Force balance |
The radial and axial force of the screw is automatically balanced. The gas force of the planetary gear requires sufficient strength and rigidity. | The screw rotor bears large radial and axial force. The screw rotor is required to have sufficient strength and rigidity. The bearing needs to bear a large load at last. |
Reliability |
The star wheel is a vulnerable part. Because of material problems, it usually has a life span of only a few thousand hours.
If it is regarded as a consumable, there will be no other reliability problems.
|
Due to the heavy bearing load, the overhaul time of most screw compressors is 20,000 to 50,000 hours. The bearing needs to be replaced and the value is high. |
Noise and vibration |
Good force balance, low noise, and vibration, generally 60~68dB(A). | Poor force balance, high-frequency noise when the rotor meshes, generally 64~78dB(A). |
Manufacturing costs |
Ordinary bearings can be used for screw and star wheel bearings. The manufacturing cost is lower. | Due to the relatively large load of the two-screw rotors, bearings with higher precision are required. The manufacturing cost is higher. |
Maintenance and repair |
It is not difficult to maintain and repair. | The maintenance of the twin-screw is very simple. As the large-scale use of the twin-screw, there are more and more technicians for the overhaul of the main engine. Currently, there is no need to return to the factory or the support of the manufacturer. |
Scope of application |
It can work under high pressure and is suitable for occasions with high exhaust pressure.
The single-screw rotor and the star wheel are in contact sealing. It is easier to achieve oil-free at low speeds.
|
It only can be used in medium and low-pressure applications, for power, refrigeration, and gas transportation. It is generally less than 4.5MPa.
Since the rotors cannot directly mesh without oil lubrication, they require a high speed (usually above 10,000 rpm). The efficiency is low.
|
Types of Rotary Screw Air Compressors
Rotary screw air compressors are also available in two primary applications: oil free and oil injected. Here’s a breakdown:
Oil Free – External gears synchronize the position of the counter-rotating screw elements, and, because the rotors do not come in contact and create friction, no lubrication is needed within the compression chamber. As a result, the compressed air is oil-free. Precision engineering within the housing keeps pressure leakage (and drops) from the pressure side to the inlet at a minimum. And because the internal pressure ratio is limited by difference in air temperature between the inlet and discharge ports, oil-free screw compressors are frequently built with several stages and inter-stage cooling to maximize the pressure reach. The gearbox driving the mechanism does contain lubricants; oil-free refers to the compression chamber itself, and the delivered air is free of foreign contaminants beyond those found inherently in the air that passes through the intake.
Oil-Lubricated – In liquid-injected rotary screw air compressors, a liquid is injected into the compression chamber to cool and lubricate the compressor elements moving parts, to cool the air being compressed in the chamber, and to help minimize leaks from returns into the chamber during discharge. While oil is the most common liquid used today because of its lubricating and sealing properties, water and other polymers are sometimes used. The oil is then separated and passes through a filter and cooler before it cycles back into the process again. The compressed air can still be hot and often times is run through a cooler, depending on end usage.
- Air enters the compressor through the inlet valve.
- Air then travels through the pressure control line and into the regulator valve. This process sets the air pressure for the system.
- Both oil and air enter the compressor, where they combine into a mist. Air travels the length of the matching rotary screws and becomes compressed.
- After exiting the compressor, the air and oil mist enters the primary oil separator tank. The tank uses centrifugal force to make the oil molecules come together, forming droplets that fall to the bottom of the tank. The oil can then be recycled into the air compressor for the next batch of air.
- The air then enters a secondary separation filter, which further purifies the air and removes more of the oil.
- The oil-free air then exits the system, into a reserve tank or the connected air tools or machinery.
- The oil travels from the separator tank to an oil cooler. Next, it goes through a filter that removes any debris and is then returned to the air compressor.
RS Series compressors combine efficient operation with outstanding durability in the most demanding environments.
STANDARD CONTROLS
Display includes discharge and sump pressure gauges, temperature gauge, hour meter, dual high air/oil temperature shutdown switches with indicating light, start-stop buttons, optional timed dual control switch, load/unload switch, standby light, power on light and optional PSID indicators.
• Modulation control
• Convenient Timed Dual control switch
• Load/Unload switch
• Hour meter & temperature gauge
• Dual high temperature shut down switches
Conveniently located with hinged access door. Built-in across the line magnetic starters with thermo overload protection ensures long motor life. 120 volt control circuit with fused protection is provided for safe operation. Standard NEMA 1 control panel comes U.L. and C.U.L. listed with electrical components U.L. and C.S.A. approved. Wye-Delta Starters are standard on 125 through 300 HP.
QUALITY COMPONENTS
Built to the highest levels of performance and reliability.
• Superior durability handles even the most demanding applications
• High-efficiency separation and filtration for long life
• Generously sized components for the utmost in reliability and maximum uptime
• Rugged sub-frame for years of trouble-free operation
SUPERIOR PACKAGE DESIGN
Robust design ensures maximum uptime.
• Open design offers easy access to all components — no need to remove panels or brackets
• Rugged and leak-free design
• Easy servicing for low cost of ownership
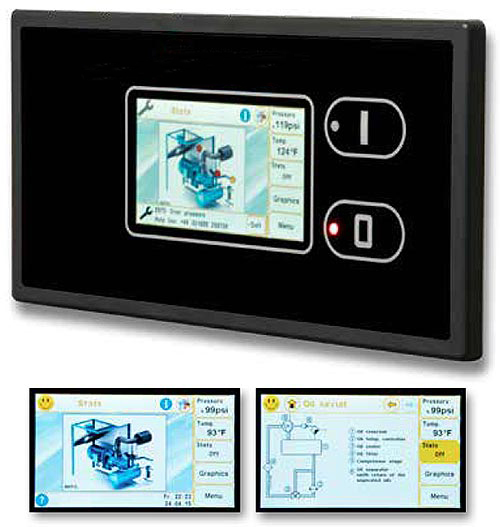
iCommand Controller
With the optional iCommand-Touch, a full-color screen displays graphs which capture and track factual, real-time air usage by the hour, day, week and month. Historical data can be retrieved at any time at the touch of the screen. Data trending keeps your finger on the pulse of your entire compressed air system. Continuously tracks pressure, temperature, air quantity and usage to easily diagnose and optimize your plant’s air system.
• Simple Touchscreen Control
• Intuitive Navigation
• Capture Real-time and Historical Data Trending
• Precisely delivers compressed air to usage
LOW POWER CONSUMPTION
Designed for outstanding efficiency.
• Exclusive slow-speed airend profile results in higher air delivery while reducing power consumption
• Proven control technology for power savings and pressure stability in all demand loads
• NEMA Premium Efficiency motors
• Low internal pressure drop increases efficiency
CUSTOMER-FOCUSED ENGINEERING
Flexibility to meet your specific needs.
• Open design allows flexibility for meeting the needs of unique applications
• Large range of factory options to fit individual needs
Modell
|
Capacity
FAD (CFM) |
Motor
|
Tank
|
Dimensions
|
Gewicht
(Unenclosed) |
|||||
---|---|---|---|---|---|---|---|---|---|---|
100 psi
|
125 psi
|
150 psi
|
175 psi
|
HP
|
Gal.
|
(L x W x H In.)
|
Lbs.
|
|||
RSB-15B
|
69
|
59
|
51
|
45
|
15
|
–
|
60 x 41 x 39
|
940
|
||
RSB-15T
|
69
|
59
|
51
|
45
|
15
|
80
|
73 x 41 x 65
|
1175
|
||
RSB-20B
|
92
|
81
|
76
|
65
|
20
|
–
|
60 x 41 x 39
|
985
|
||
RSB-20T
|
92
|
81
|
76
|
65
|
20
|
120
|
73 x 41 x 65
|
1305
|
||
RSB-25B
|
111
|
101
|
92
|
84
|
25
|
–
|
60 x 41 x 39
|
1060
|
||
RSB-25T
|
111
|
101
|
92
|
84
|
25
|
120
|
77 x 41 x 69
|
1380
|
||
RSB-30B
|
135
|
125
|
113
|
101
|
30
|
–
|
60 x 41 x 39
|
1150
|
||
RSB-30T
|
135
|
125
|
113
|
101
|
30
|
120
|
77 x 41 x 69
|
1420
|
||
RSB-40B
|
189
|
173
|
150
|
140
|
40
|
–
|
72 x 53 x 44
|
1425
|
||
RSB-40T
|
189
|
173
|
150
|
140
|
40
|
200
|
80 x 53 x 81
|
1745
|
||
RSB-50B
|
220
|
204
|
186
|
170
|
450
|
–
|
72 x 53 x 44
|
1600
|
||
RSB-50T
|
220
|
204
|
186
|
170
|
450
|
200
|
80 x 53 x 81
|
1920
|
What makes AGKNX being the best Screw Air Compressor Suppliers in China
Safe and convenient
Rotary screw air compressors are incredibly convenient given that they deliver the needed air without stopping, and these cases of accidents with machines are almost unheard of.
Longevity
Our compressors are well-known for lasting over hours working continuously over years. They’re built to last and work hard so your business can keep running smoothly. And you won’t have to worry about downtime with our reliable equipment.
Made up of high-quality material
We have the best screw compressors in the world and they are made to last for a long. Our compressors are designed with high-quality materials that will make your work easier and more productive. Moreover, due to the strong build, we ensure you won’t have to worry about maintenance or repairs and can last over hours of continuous use.
Easy to maintain
The Agknx Sigma profile airend provides 20-30% savings over comparable size competitive compressors. These compressors are direct drive with easily cleaned coolers and the innovative & resourceful Sigma Control 2 for ultimate energy conservation and maintenance information.
Cost-efficient option
Enhancing the technology and function we provide you with a more efficient product that will save you money in the long run. So, you won’t have to worry about high maintenance costs or expensive repairs because of our durable design.
Produce less noise
Rotary screw compressors are the quietest performers of all. As they’re not huge in size and have noise-dampening technologies that make them even more convenient to store anywhere. Aside from quiet operations, they provide a safe working environment.
Apt for any kind of use
We manufacture different variants of screw air compressors that can be used for hefty industrial mechanisms that require gases in higher volumes and pressure. Being the top manufacturer of the screw compressor it’s our responsibility to provide our air compressors with world-class reliability.
Our range of Compressors
- Screw compressor
- Scroll compressor
- Oil-free compressor
- Oilless compressor
Achieve Your Goals
Company Concept
Company adhering to the management objective of quality first, prestige supreme.
Strong Technical Force
Strong technical force, superior to similar products in Japan and Germany, please refer to vacuum pump comparison for more detailed information. Advanced production and testing equipment, strict implementation of ISO9001 quality management system, products have obtained CE certification, and the ep series have passed US authoritative testing and certification
24/7 Customer Support
24×7 service support is one of the best services in the company. 24×7 service support providing quality services at anytime, anywhere in the world.

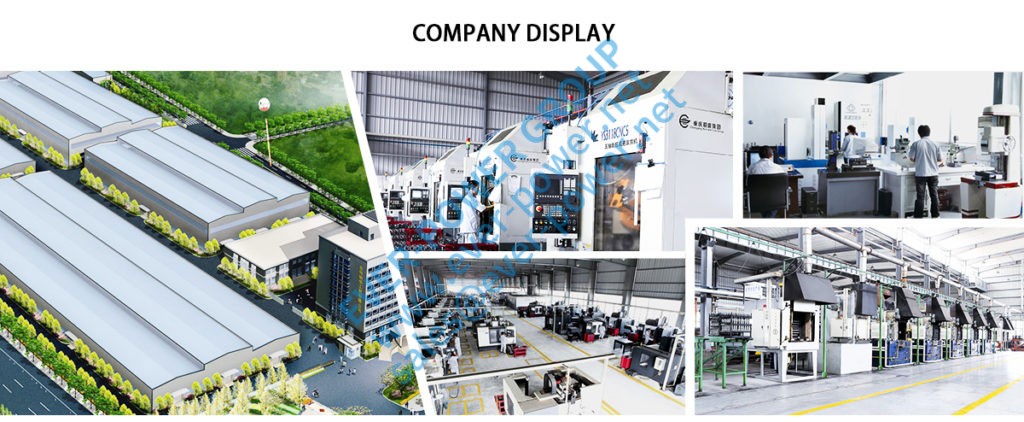
We’ve built up an excellent reputation over time by providing quality products at competitive prices with outstanding customer service. So, if you require modern equipment then you’ve come to the right place. To check out our collection visit us https://roots-vacuum-pump.com/vacuum-pumps/
Start a conversation with us by email at [email protected]
Ready to get started?
Keep in touch or order products